Her new “Ocean” collection was inspired by Myanmar’s traditional articulated fish jewelry, with depictions of flounder, catfish, and more.
Jewelry Designers’ Production Grinds to a Halt in NYC, Los Angeles
Meanwhile, international production is turning into a saving grace.
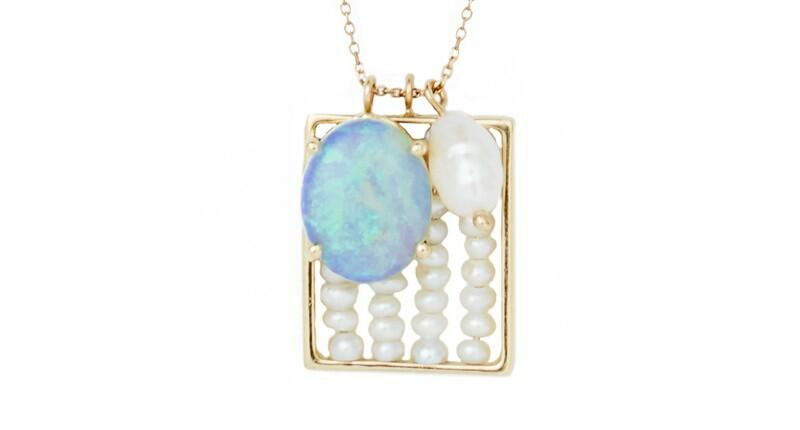
New York—Within a week, the COVID-19 global health pandemic has forced domestic jewelry production to a halt.
“It’s pretty much entirely stopped in New York,” said David Hakimian, founder of DEH Jewelry Solutions, a fine jewelry production management and design development company that currently works with about 15 brands.
A week ago, Hakimian painted a very different picture of the New York City Diamond District, with manufacturers making their own decisions about employee schedules to facilitate social distancing.
At that point, New York state had yet to enact its executive order closing nonessential businesses.
So while Hakimian’s team of four was working from home last week, coordinating production between various manufacturing partners remotely, the Diamond District was almost fully functional, with the only real delay due to casting companies that made the decision to close.
“Ninety percent of jewelry makers [in the New York City Diamond District] take work home. It’s incredibly common in the jewelry industry in general.” — David Hakimian, founder of DEH Jewelry Solutions
Other members of the jewelry-making supply chain were getting creative to stay operational.
Hakimian explained: “Ninety percent of jewelry makers [in the New York City Diamond District] take work home. It’s incredibly common in the jewelry industry in general. Almost all Diamond District company employees have a full bench set up at home and, even outside of crisis, take work home on nights and weekends.”
The exception is casting companies, which use equipment too technical and expensive to set up in a typical residence, not to mention the security risk of having large amounts of gold and platinum on hand.
Aside from closed casters, several of the manufacturers Hakimian works with had employees working from home in some capacity last week to avoid contact at work.
“The hard part is the logistics of moving things around,” he said. “A piece needs to move from one person to another to get completed.”
Some Diamond District manufacturers, Wwake designer Wing Yau confirmed, were staggering their employees in different shifts.
In the last year, Wwake’s 14-person company has transferred the manufacturing of standard styles to jewelers in the District, allowing the current team of three jewelers to focus on one-of-a-kind and custom pieces at the company’s Brooklyn studio.
As Wwake’s manufacturing partners transitioned to working in shifts and taking work home last week, the Wwake team dispersed to their various apartments, with jewelers
“We got lucky that we had someone with that ability,” said Yau. “Our biggest concern was getting people off of public transportation.”
Wwake’s new way of working has mirrored much of the Diamond District’s, with a flexible, make-it-work attitude.
“I think a lot of jewelers can work from home, and that’s what we’re finding with our team and with our contracted partners,” she said.
“We prepped as much as we could to be done before we moved into our home studios, focusing on things that don’t need torches or our laser welder, like assembly, finishing and cleaning castings, polishing them. We’re saving everything else that requires fire, so any type of soldering and welding, to be done in the studio.”
As of last week, morale was high, Yau said, with her team working in the spirit of coming together, being careful to transfer items between each other’s apartments wrapped in plastic and left in doorways, rather than handed to co-workers.
“I want to express how grateful I am for us to have the opportunity to be able to make things in our homes and still be able to connect with people putting that work out there. I think a lot of it has to do with being so small and so nimble and having everything always at the tip of our fingers,” she said.
West Coast Precursor
California’s shelter-in-place ordinance, announced Thursday evening and enacted immediately, provided a clue to what was coming to New York City.
For the downtown L.A. Jewelry District, the decision to close was made for jewelers, as several of the buildings housing a majority of manufacturers closed Friday, essentially locking jewelers out.
Prior to the shelter-in-place order, “everyone was working harder than usual to finish orders,” said designer Lizzie Mandler, “not knowing when everything would shut down.”
The mood had been uneasy for about two weeks prior and Mandler, whose office is not in the Jewelry District, had been handling production herself because her employees weren’t comfortable going downtown. (Her team began working from home the week of March 16.)
“I want to continue production to keep my manufacturers afloat, but I’m OK not actively producing right now because stores aren’t actively buying.” — Lizzie Mandler, jewelry designer
Mandler was last in the Jewelry District last Wednesday, March 18 and was able to complete 90 percent of her store orders, she said, plus she personally finished a number of engagement rings and wedding bands she was due to ship out.
She planned to come back Friday to finish up loose ends but was too late.
“People have been understanding and accepting of the situation, which I feel is a blessing,” she said.
She also feels fortunate that, while she was in the hiring process for new positions at her company, she hadn’t yet brought any new employees on board.
Mandler works with about 15 different manufacturers, using different artisans for different skills, and knows of some who have had to lay off employees so they can collect unemployment, with hopes to rehire once business is up and running again.
As coronavirus fears ramped up in recent weeks, Mandler wisely didn’t reorder any of the best-selling styles she tries to keep in stock.
“I want to continue production to keep my manufacturers afloat,” she explained, “but I’m OK not actively producing right now because stores aren’t actively buying.”
To fulfill her direct ecommerce orders she’s selling the inventory she has, fresh from Paris market week, and shipping from her apartment.
“Production is scary because it’s an upfront investment,” said Mandler. “We pay for it way before we ever see the money stores pay for it, generally. I think all of that is going to change for a while. My planning is that it will hopefully go back to normal for holiday.”
Sydney Evan founder and designer Rosanne Karmes also “saw the writing on the wall,” with California’s impending shelter-in-place ordinance.
Up until that point, “Fortunately I hadn’t been affected in the ways of production at all,” she said, “[but] I work mainly by instinct, more than anything else. I started to say, ‘we need to make some changes as soon as possible.’”
Last week, most of her 35 employees began working from home in order to observe social distancing recommendations, with the exception of four to five operational staff who finished things up in the office, like accounting and shipping orders.
Karmes’ intuition proved prescient—her showroom and office are located in one of the main Jewelry District buildings that was locked on Friday.
“My number one concern is the safety of everyone who works for me. Even if the buildings stayed open, there wouldn’t be anyone to come in and ship.”
On Sunday at 8 p.m., New York State followed suit, enacting its ordinance that closed down all nonessential businesses.
“Now everyone, at least in New York, is closed,” said Hakimian, even the holdout casting companies.
“Things are more or less at a halt. People who have taken things home are able to finish things up, but people live all over between the various boroughs and New Jersey,” making getting items between craftspeople via messengers costly and slow.
Wwake’s team continues to work from home, and several of their Diamond District manufacturers are doing the same, to the best of their abilities.
True to the company’s nimble nature, it’s even found a new caster to work with for the time being in Virginia, though the Wwake team is not sure how long that company will be operational either.
Overseas Solution
Diversifying production has proven beneficial to several designers.
The bright spot in Sydney Evan’s production has been Thailand, where they produce in addition to L.A.
“So far, there hasn’t been a single problem [with production there],” said Karmes.
Throughout COVID-19’s worldwide spread, the company hasn’t experienced a single delay from its Thai partners, whose staffs are still working.
"Everything overseas was a complete mess six weeks ago and now we're relying on them to save us in some aspects.” — David Hakimian
Karmes’ fear is how the halt to L.A. production will negatively impact her Thai manufacturers. “We definitely had to cancel some orders with our factory,” she said. “This is going to be quite a ripple effect.”
Of Hakimian’s 15 clients, “Everyone produces domestically in some capacity [but] everyone’s generally diversified so they aren’t too reliant on one person or location.”
Hakimian noted some of his brands that produce in China were quick to shift to their New York manufacturers as the coronavirus took hold of the country earlier this year.
Now, they’re doing the opposite.
“China is more or less fully operational," he said. "Everything overseas was a complete mess six weeks ago and now we're relying on them to save us in some aspects."
That manufacturing flexibility has been crucial to Dana Gordon, head of Dana Rebecca Designs.
Gordon’s family owns a manufacturing business in Chicago, where she executes most of DRD bridal, and produces the rest of her collection in China and India.
“We’re really lucky that a lot of our manufacturing facilities that are overseas are an extension of our family,” she explained, going back generations with her own family.
Coronavirus spread has moved her production between manufacturers. China, which was shut down for much of February, is now fully operational, just as India has enacted a 21-day lockdown.
“We got over the hump of those production issues [in China] and now India has closed,” said Gordon. “My worry is the ebb and flow. No one is on the same timeline.”
Her Chicago manufacturing is closed, per city and state guidelines, and her administrative teams in Chicago and New York are now working from home.
Personally, she’s still shipping out orders from her apartment.
“What’s set our brand apart is we stock the majority of our products pretty heavily,” she explained, delivering customers “instant gratification.”
“For our bread-and-butter pieces in our core collection under $600 we have a couple hundred in every style, colorway and length.”
After a strong holiday season, Gordon had restocked even more pieces than usual, which is coming in handy now, even as shipments still come in from overseas.
“It’s a day-to-day situation,” she said, “[but] we’re diversified in a healthy way to weather the storm.”
She said the next new collection is on hold as she focuses on selling the stock her company has.
“Retailers aren’t worried about newness,” she pointed out, “they’re worried about stock they own.”
Gordon said as the coronavirus situation continues to change there’s no telling what’s next, but Mother’s Day, the company’s second biggest holiday after Christmas/Hanukkah, will be a good barometer of consumer sentiment.
The Latest
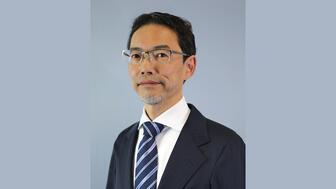
Longtime Casio executive Yusuke Suzuki is the new president and CEO of Casio’s U.S. subsidiary.
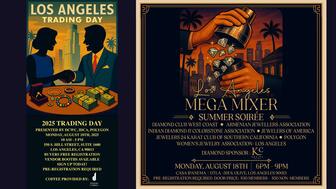
The full-day sourcing and networking event, slated for Aug. 18, will be followed by the fifth annual Mega Mixer Summer Soirée.
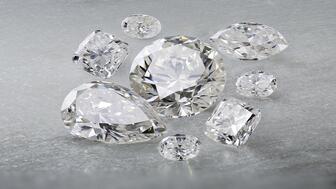
As a leading global jewelry supplier, Rio Grande is rapidly expanding and developing new solutions to meet the needs of jewelers worldwide.
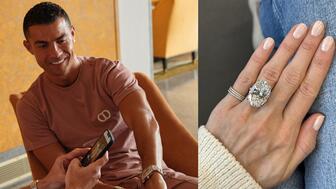
Model Georgina Rodríguez received a rock of an engagement ring, with her diamond estimated to be 35 carats, experts say.
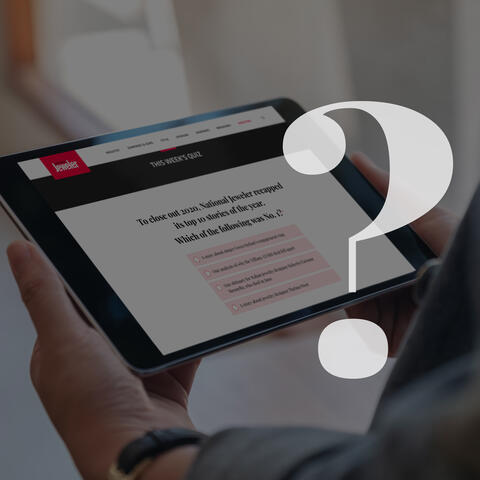
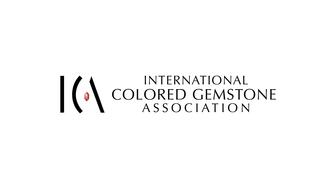
The board elected 9 new directors at its recent ICA Congress in Brazil.
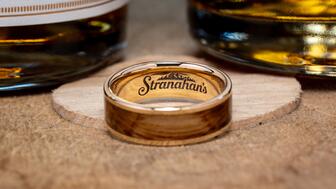
Three winners will receive a custom ring from Honest Hands Ring Co. inlaid with a piece of history from Denver-based distillery Stranahan’s.
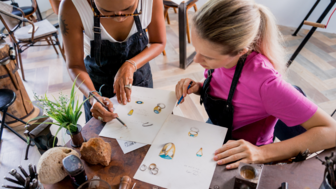
The Seymour & Evelyn Holtzman Bench Scholarship from Jewelers of America returns for a second year.
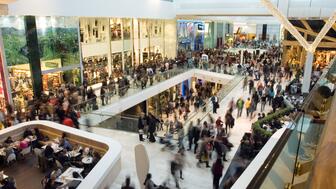
JD Sports and Wawa were among the fastest-growing retail companies in the U.S. last year.
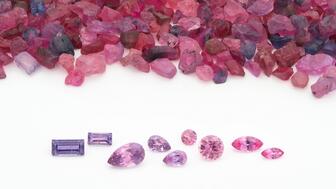
The new inventory, all untreated, features vibrant hues and unique bicolor combinations.
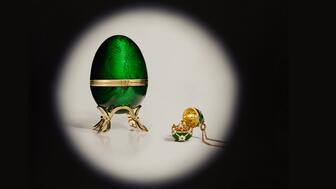
Acquired by a tech investor, the historic brand will continue to focus on jewelry, accessories, and timepieces.
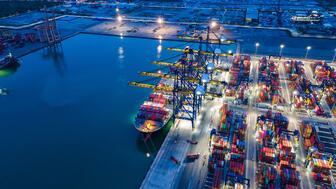
President Donald Trump issued an executive order extending the pause on higher tariffs to November as negotiations with China continue.
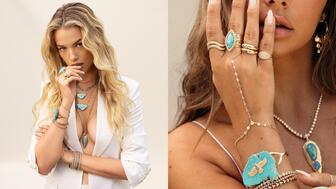
The “Thunderbird Slab” collection features a thunderbird motif as a symbol of power, protection, and boundless possibility.
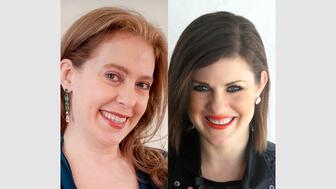
Columnists Jen Cullen Williams and Duvall O’Steen share tips on how to elevate your professional image.
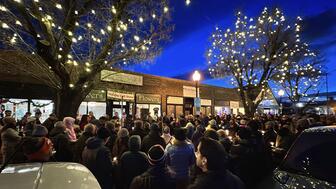
Peter Damian Arguello, a jeweler in the Denver suburb of Wheat Ridge, was found dead inside his store in November 2023.
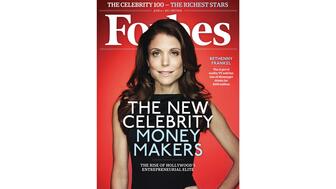
The Continental Buying Group’s 2025 Tampa Experience Show is slated for Sept. 8-10.
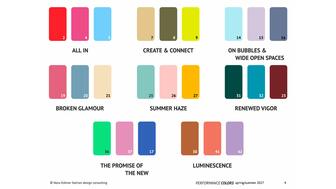
Associate Editor Lauren McLemore recently attended a fabrics trade show where a trend forecaster shared her predictions for summer 2027.
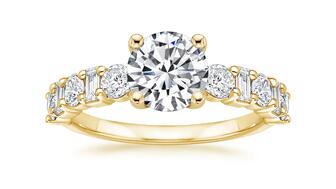
The company raised its full-year sales guidance while noting it has not yet assessed the potential impact of the latest tariff news.
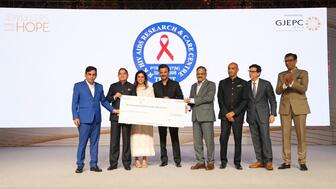
The organization has raised more than $1.3 million for charity since its inception.
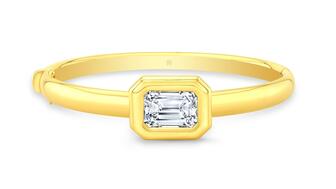
The brand’s latest iteration of a bezel-set diamond bangle features clean lines and a timeless design for a new modern silhouette.
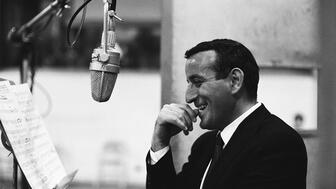
The first watch in the series commemorates his participation in the Civil Rights movement, marching from Selma to Montgomery in 1965.
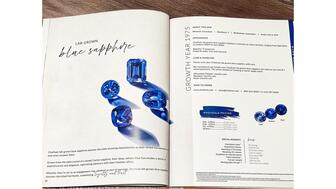
The catalog contains a complete listing of all the loose gemstones in stock, as well as information about the properties of each stone.
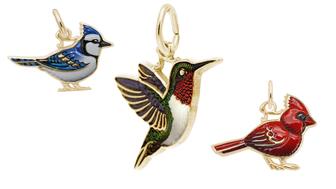
The company added a retailer dashboard to its site and three new birds to its charm collection, the cardinal, blue jay, and hummingbird.
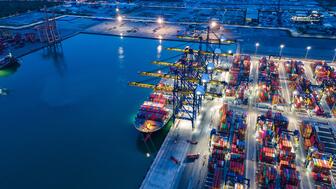
An additional 25 percent tariff has been added to the previously announced 25 percent.
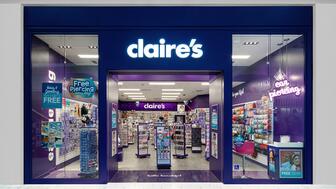
The jewelry and accessories retailer plans to close 18 stores as part of the proceedings.
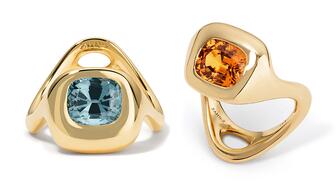
Designer Hiba Husayni looked to the whale’s melon shaped-head, blowhole, and fluke for her new chunky gold offerings.
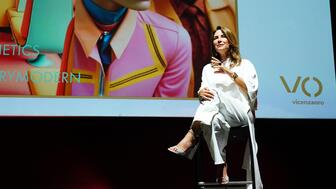
She will present the 23rd edition of the trend forecasting book at Vicenzaoro on Sept. 7.